News
KYOCERA Introduces New Industrial Cutting Tools for Cast Iron Machining
Kyocera MFK milling tools reduce costs, improve quality in machining workpieces of complex-shaped cast iron
Hendersonville, NC, March 9, 2015 - Kyocera Precision Tools, Inc. today unveiled its new MFK indexable milling cutter for cast iron, a milling system that will allow machinists to reduce costs and improve their milling operations through the use of double-sided, 10-edge negative inserts.
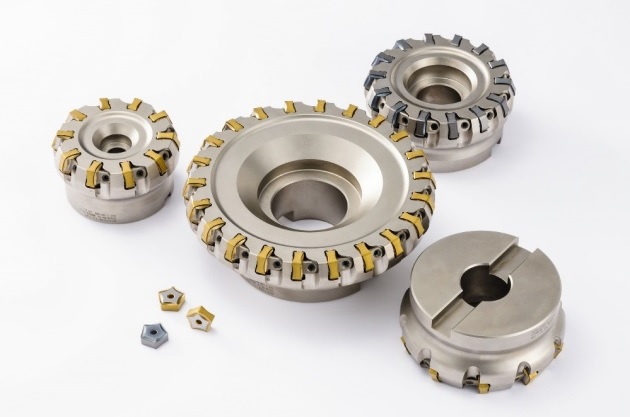
Kyocera's new MFK indexable milling cutters with negative inserts improve machining quality of cast iron by reducing cutting forces and preventing chipping.
Development BackgroundAutomotive engines, construction equipment and machine tools require metal components in complex shapes that are commonly created by casting molten metal in specialized molds. Castings taken from these molds require difficult finish machining. Many workpieces are challenging to hold securely during the machining process because their complex shapes limit clamping rigidity. Insufficient clamping rigidity causes vibration and chattering due to the cutting forces of the machining process. In addition, cast iron workpieces are susceptible to a phenomenon known as "breakout," in which the edge of the workpiece chips away rather than being cut cleanly. Cutting tool inserts that can improve machining quality by reducing the cutting forces and preventing chipping are therefore in great demand.
New Product Outline
Kyocera's new MFK cast iron milling cutter utilizes a newly developed double-sided insert with 10 cutting edges. Although negative inserts offer cost benefits because cutting edges can be formed on both sides of the insert, they tend to increase cutting resistance, causing a decrease in sharpness or an increase in chattering. To address this challenge, Kyocera has developed uniquely shaped inserts using its proprietary molding technology, which reduces both cutting resistance and chattering. The inserts also improve machining quality through a double-edge structure in which two cutting edges are provided for the insert corners.
Kyocera's MFK milling cutters offer improved quality and better cost performance in machining cast iron, with higher productivity in conditions ranging from roughing to finishing.
New Product Features
1. Double-sided, 10-corner negative inserts provide quality and cost benefits
1-A. Proprietary edge shape reduces cutting resistance
The newly developed negative inserts utilize two lead angles per corner. Using molding technology developed by Kyocera, a large axial rake angle is provided on cutting edges, reducing cutting resistance and facilitating smoother machining. Increasing the lead angle also reduces cutting resistance in an axial direction of the workpiece, vibration and chattering.
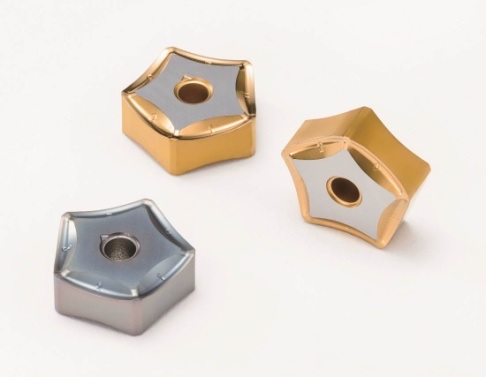
1-B. Double-edged structure helps prevent inserts from fracturing and breakout
A proprietary double-edged structure using two main cutting edges is utilized on each corner to cushion initial shock at the moment of workpiece contact — the onset of cutting. This helps prevent inserts from fracturing and breakout, helping to stabilize the machining process and improve finish quality.
2. Newly developed CVD material for cast-iron milling offers long tool life and stable machining
Kyocera has added the new CA420M CVD*1 material for cast iron milling to its insert grade lineup. CA420M is comprised of a newly developed, high-toughness base substrate with a new CVD coating developed using proprietary crystal-control and film-formation technologies. Improved abrasion resistance, essential in machining cast iron, will allow CA420M to deliver better cost performance, longer tool life and a more stable machining process.
3. Accommodates a wide range of cast-iron machining conditions, from roughing to finishing
Kyocera's extensive lineup of milling cutters, insert shapes, and grades ensures an ideal combination to cover a wide range of conditions, from cast iron roughing to finishing. The MFK family of products is comprehensively designed to help improve customer productivity.
*1 The Chemical Vapor Deposition coating method allows multiple layers of different materials, resulting in thicker film.
Kyocera Precision Tools, Inc.
102 Industrial Park Road
Hendersonville, NC 28792
PH: 800-823-7284
email: cuttingtools@kyocera.com
website: kyoceraprecisiontools.com
About KYOCERA
Kyocera Precision Tools, Inc. is headquartered in Hendersonville, NC, with production facilities there and in Costa Mesa, CA and Wapakoneta, OH. The company provides specialized cutting tools for the aerospace, medical, automotive, general machining, power generation, printed circuit board and steel markets.
Kyocera Corporation (NYSE:KYO) (TOKYO:6971), the parent and global headquarters of the Kyocera Group, was founded in 1959 as a producer of fine (or "advanced") ceramics. Kyocera specializes in combining these engineered materials with other technologies to create cutting tools, industrial components, electronic devices, semiconductor packages, solar power generating systems, printers, copiers and mobile phones. During the fiscal year ended March 31, 2014, the company's consolidated net sales totaled 1.45 trillion yen (approx. $14.1 billion USD). Kyocera appears on the latest listing of the "Top 100 Global Innovators" by Thomson Reuters, and is ranked #531 on Forbes magazine's current "Global 2000" listing of the world's largest publicly traded companies.